What is etching (photo-etching process)?
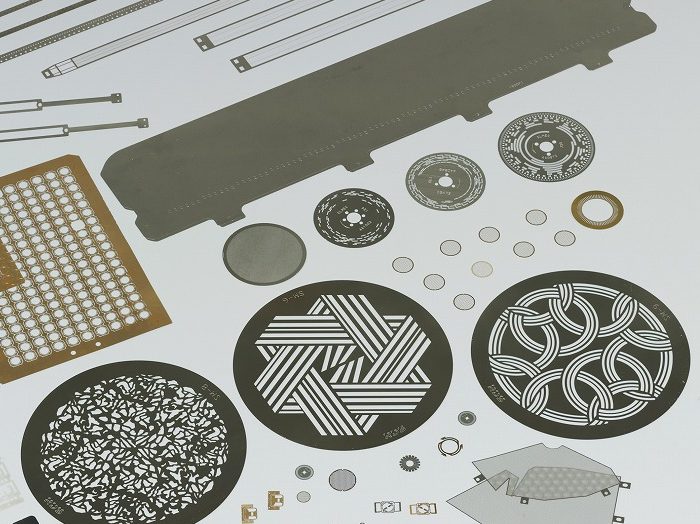
Principle: Protoengraving technology is used to make patterns on metal by masking areas with a protective film and then dissolving and removing unwanted parts with an etchant to create the desired shape. (For details, please refer to the “Etching Process” section)
Meltec uses this precision etching technology (photo etching) to process thin metal sheets and manufactures precision parts for industrial use.
Industrial application fields: Electronic parts, electrical parts, automotive parts, medical equipment, optical equipment, office equipment, etc.
Processable materials
Metal materials: Stainless steel (SUS), copper (Cu), iron (Fe), nickel (Ni), nichrome (NCH), and others
Special metal materials: Molybdenum (Mo), titanium (Ti), aluminum (Al), tungsten (W), and others
Advantages of the etching process
- High-precision processing with no burrs, distortions, or work hardening.
- Drastic reduction of initial cost as no expensive tooling is required, unlike press work.
- Ideal for prototypes as shorter production and delivery times are possible.
- Suitable for mass production, as many pieces can be processed simultaneously.
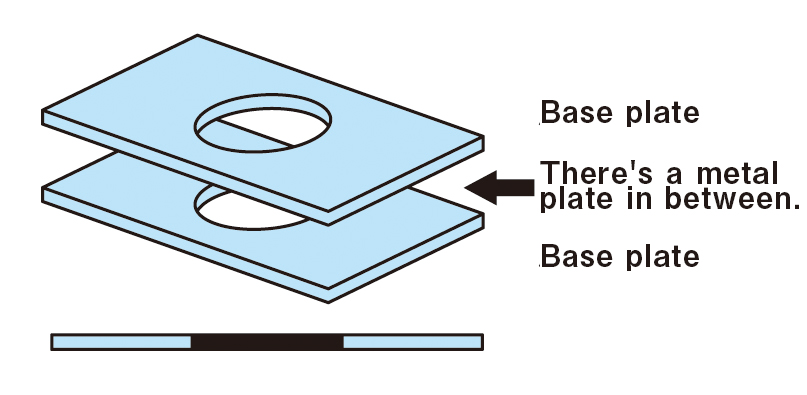
1、Making the original etching plate
Based on the drawings and data, we create the original plates in CAD. The original plate is the key to dimensional control and quality.
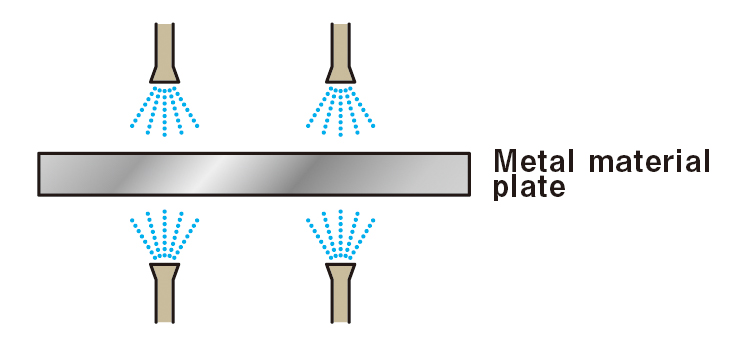
2、Dewaxing and cleaning of metal plate materials
Metal sheet materials such as stainless steel and copper are processed. The pre-treatment is a degreasing cleaning to remove oil and foreign matter from the metal surface. This is to improve the adhesion strength during the next process of lamination.
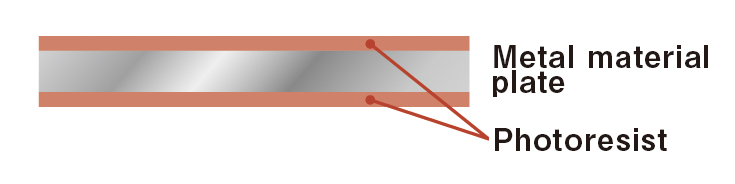
3、Resist lamination
Apply photoresist to both sides of the metal sheet material. Now, the masked (protected) part will not be etched.
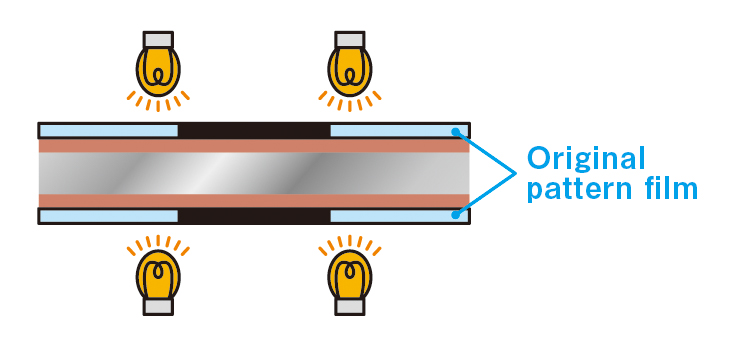
4、Bake the pattern by exposure
The original film is placed on the laminate and exposed to UV light. The unshaded portion of the photoresist is sensitized and the pattern shape is transferred. This is done in a clean room for precision pattern reproduction and quality control.
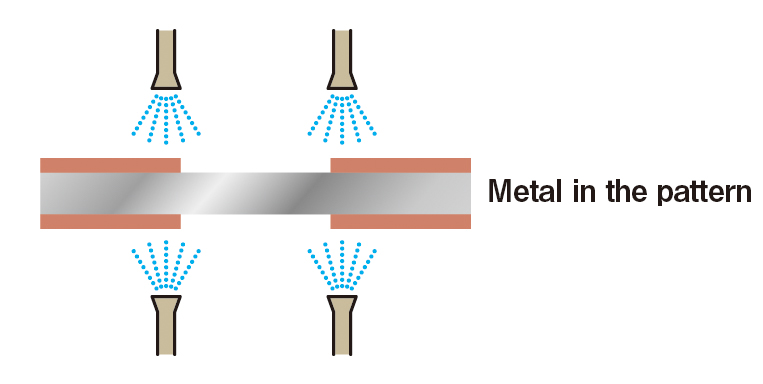
5、Development process
The pattern (shape) of the original etching plate is developed on the metal material to which the exposure is transferred. The surface of the metal plate is exposed by removing the resist from the unnecessary patterned area. The masking of the etching pattern in the next process is completed.

6、Etching
Etchant is sprayed on the masked metal plate material. Only the metal parts exposed by the development process are etched (corroded, dissolved, and removed), so that the metal plate is removed to the patterned shape.
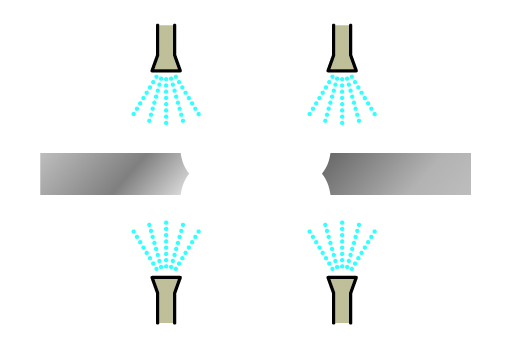
7、Resist stripping
After the etching process, masking by photoresist remaining on the surface of the metal plate is removed, and then it is washed and dried.
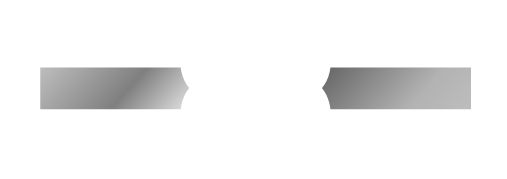
8、Product inspection
External and dimensional inspections are performed.
Meltec’s etching process
In addition to general etching, Meltec offers a wide range of services, from precision etching using our unique technology to the processing of difficult-to-cut materials and difficult-to-machine shapes. We can also add new shapes and functions by applying composite processing and surface treatment after the etching process under our integrated in-house system.